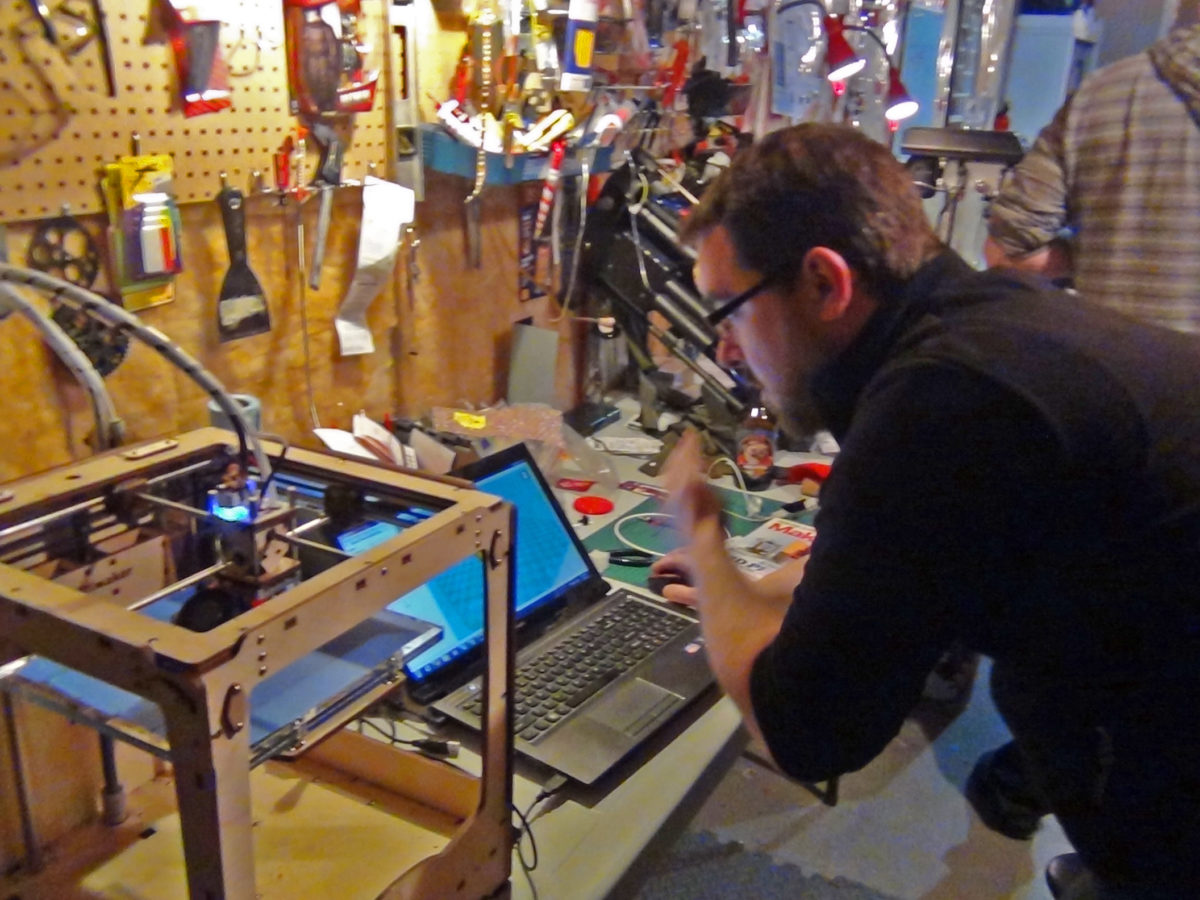
Moving along two arms that operate like pistons, a nozel draws a square with molten plastic. The square is then filled in with a mesh pattern. It repeats, with slight variations, layering the plastic until a cube is formed.
This is the basics of 3D printing, and Fredericton’s burgeoning techy class believes it is going to play a big role in the future of manufacturing.
A group got together Wednesday night to organize the Fredericton Makerspace, where they have access to the machines, and other means for designing and production.
“Instead of going to the store to buy product X, Y, or Z, you’re going to be able to buy the file online and print out the product in your home,” said Rick McCaskill.
McCaskill is the proud owner of an Ultimaker 3D printer, which is set up in his basement shop. When he bought it two years ago, it was one of the first in Fredericton.
Members of the Fredericton “maker” community meet in McCaskill’s basement workshop every Thursday, often to work on projects that make use of their talents in engineering, design and electrical.
Sometimes the group gathers in the shop to just talk and hang out. Recently there has been a hot topic: The Makerspace.
Philip LeBlanc gave the keynote speech at the Makerspace meet-up. Afterwards, he mingled with the crowd and drummed up support for the cause.
He was one of the first to visit McCaskill’s shop about six months ago, and has an enthusiasm to bring Fredericton’s makers together under one roof.
“A maker is anybody who wants to take the power into their own hands. They don’t want to buy a product, they want to make it,” he said.
“Basically it’s enabling the creative class to take their ideas and bring them to life without any hesitation.”
LeBlanc wants to take the concept of McCaskill’s weekly gatherings and make it into a full-time open-house, stocked with all the information, equipment, and talented people one could need to create almost anything.
An Ultimaker costs about $2500 assembled. When McCaskill bought his, you could only buy it in a kit. He needed a lot of help from a friend experienced in electrical work to assemble it. Soon, McCaskill believes, they will be a household item. As prices go down and plug-and-play ability goes up, the less technically inclined may be willing to buy.
The technology is best suited for simple items, especially customized ones. At the cost of about ten cents per minute worth of plastic filament, it’s relatively cheap to make something for yourself, but not cheap or fast enough for mass production.
Commercial 3D printers have been used to make prosthetic arms and makeshift guns, patch up human skulls, and have even been adapted to print biological matter like skin and bone.
McCaskill brings his Ultimaker to New Maryland Elementary, his daughter’s school, to show the kids.
“They get it right off the bat,” he said. Using simplified 3D design software, the kids are given the opportunity to create something, send it to McCaskill and have it printed off for them.
“I had one kid say, ‘I’m going to design something and print it out, and I’ll keep it for myself and nobody else can have it. It’ll be completely my own.’ So I asked him, ‘what if you took your design and you put it on the Internet and kids all over the world started playing with the toy you made?’ His jaw hit the floor – he’s in grade four – and his eyes lit up, and it was like a totally different way of thinking about things for him. It was awesome.”
But that’s exactly the kind of thinking these machines provide room for. Objects can be shared over the Internet in the same way words or ideas are. The push for open-source everything is on its way.